43. Hagener Symposium 2025
27./28. November 2025
„PULVER | METALLURGIE | ZUKUNFT“
Tagungsort und Tagungsbüro
Stadthalle Hagen, Wasserloses Tal 2, 58093 Hagen
Tag(e)
:
Stunde(n)
:
Minute(n)
:
Sekunde(n)
Über das Hagener Symposium
Fachveranstaltung für Innovationen und Anwendungen in der Pulvermetallurgie
Die Veranstaltung richtet sich nicht nur an Fachleute aus der Industrie, sondern auch an Wissenschaftler, Nachwuchsforscher und Studierende, die sich mit der Pulvermetallurgie und ihren vielfältigen Anwendungen auseinandersetzen. Von den neuesten Innovationen in der Elektromobilität und Windkraft bis hin zu den Fortschritten in der Medizintechnik – das Symposium deckt eine breite Palette zukunftsweisender Themen ab.
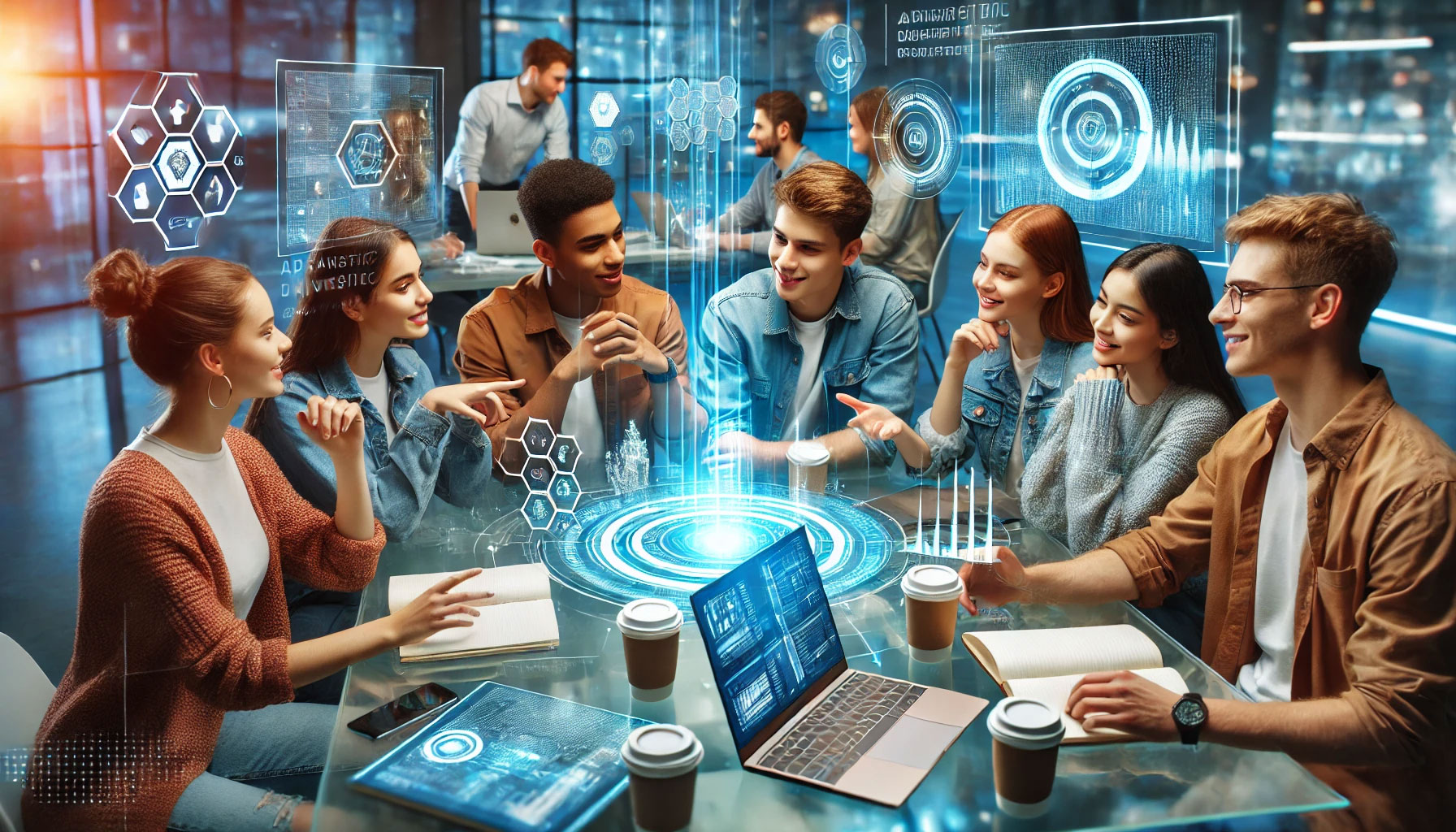
Programm
Donnerstag, 27.11.2025
9.00 h Begrüßung und Eröffnung
Vorsitzender des Ausschusses für Pulvermetallurgie
9.15 h Laudatio SKAUPY-Preisträger 2025
9.30 h SKAUPY-Vortrag: Zeitabhängige Brucherscheinungen durch Spannungsrisskorrosion an hochfesten Sinterstählen - Ursachen, Bewertung und Vermeidung
Ausfälle von kritischer Infrastruktur durch Spannungsrisskorrosion führen zu einem erheblichen volkswirtschaftlichen Schaden. Durch das zeitverzögerte, spontane und kaum vorhersagbare Versagen (verzögerter Bruch, Sprödbruchgefahr) besteht hier akute Gefahr für Leib und Leben. Das Zusammenwirken von hohen statischen Zugmittelspannungen (statische Vorspannung), einem korrosiv wirksamen Elektrolyten (Medium) und einem anfälligen, harten bzw. martensitischen Gefüge (Material) ist aber nicht nur auf Spannbetonbrücken, wie zuletzt medienwirksam bei der Carolabrücke über die Elbe in Dresden oder der Ringbrücke am Damaschkeplatz in Magdeburg diskutiert, beschränkt. Auch aktuelle Bauteile aus hochfesten Sinterstählen werden z.T. unter einem ähnlichen Regime beansprucht. Hohe statische Zugmittelspannungen können sich konstruktiv als Folge von Press- oder Schraubverbänden oder auch als Eigenspannungen aus der Prozessierung einstellen. Vergütete (klassisch vergütete, schroffgekühlte, einsatzgehärtete usw.) Gefügezustände mit Zugfestigkeiten von etwa Rm > 800 MPa reagieren dabei mitunter extrem auf das Einwirken des entsprechenden – leider nicht immer identifizierbaren bzw. vermeidbaren – Elektrolyten. In-situ bei der Korrosion gebildeter atomarer Wasserstoff führt über den HEDE-, HELP- bzw. AIDE-Mechanismus zu einer Form der Wasserstoffversprödung, die den Werkstoff weit unterhalb der klassischen Zugfestigkeit Rm versagen lässt. Neben der Gefährdung von aktuellen Bauteilen aus hochfesten Sinterstählen muss an dieser Stelle auch in die Zukunft antizipiert werden. Wir wissen nicht genau, welche neuen Bauteile und Herausforderungen (z.B. der Ammoniak- und Wasserstoffwirtschaft) im Zuge der Erzeugung erneuerbarer Energien und der Dekarbonisierung der Industrie-prozesse auf die PM-Branche zukommen werden. Daher ist die Aneignung eines Grund-lagenwissens zur Spannungsrisskorrosion und deren Ursachen, Bewertung und Vermeidung erstrebenswert. Mögliche Vermeidungsstrategien müssen bei mindestens einem der drei Faktoren (statische Vorspannung, Medium und Material) ansetzen. In der vorliegenden Abhandlung werden daher potentielle, als wirksam betrachtete Nachfolgeprozesse wie Lackieren, Dampfblauen und Ölinfiltrieren, Ölinfiltrieren und Kugelstrahlen, Zinkthermodiffusions-behandeln und Passivieren usw. auf ihre Wirksamkeit hin untersucht. Die Einflüsse der Dichte und der Mikrostruktur werden ebenfalls mit in die Betrachtungen einbezogen. Ergänzend werden die Ergebnisse mit fraktographischen und messtechnischen Befunden zum Bruchverlauf und zur Wasserstoffkonzentration korreliert und diskutiert.
10.00 h Nachhaltige Wärmebehandlung in der PM-Industrie durch den Einsatz von Wasser-stoffbrennern sowie einer dynamischen CO2-Überwachung und KI-basierter Qualitätsvorhersage
Grüner Wasserstoff ist eine nachhaltige Lösung, um Wärmebehandlungsprozesse in der PM-Industrie nachhaltiger zu gestalten. Wasserstoff wird bzw. kann in Wärmebehandlungsanlagen als Brenngas zur Ofenbeheizung, als Ofenatmosphäre oder in der thermischen Nachverbrennung (TNV) als Wärmequelle eingesetzt werden. Hierdurch kann der Einsatz von umweltschädlichem Erdgas (Methan) reduziert oder ganz substituiert werden. Zudem verbrennt Wasserstoff ohne CO2-Freisetzung. Neben dem Einsatz von Wasserstoff ist die dynamische Überwachung der Ofenatmosphäre und der damit einhergehenden CO2-Emission entscheidend für die Optimierung und die nachhaltige Gestaltung von Wärmebehandlungsprozessen. Der Vortrag gibt einen Überblick über aktuelle Aktivitäten innerhalb der BleiStahl Gruppe zu diesen Themen. Der Fokus liegt hierbei auf dem Einsatz von Wasserstoff als Brenngas in der TNV, der dynamischen Prozessdatenerfassung und der Auswertung der Daten mittels moderner KI-Methoden.
10.30 h Kurzpräsentation einzelner Aussteller, anschließend Besichtigung der Ausstellung und Kaffeepause
11.30 h Neue Pulvermaterialien für die Laserbasierte Additive Fertigung - DFG-Schwerpunktprogramm 2122
Laser in der Produktion werden immer leistungsfähiger und brillanter, jedoch sind für die aktuell geforderten Bearbeitungsaufgaben die verfügbaren Materialien oftmals vollkommen unzulänglich. Bis heute werden in der additiven Fertigung Metallpulver eingesetzt, die vor über 50 Jahren für ein völlig andersartiges Verfahren – das thermische Spritzen – entwickelt wurden. Bei modernen laserbasierten additiven Verfahren führen diese Pulver jedoch zu Prozessinstabilitäten sowie Porositäten und Defekten im Bauteil. Im Bereich der Polymerpulver fehlt es zudem an einer breiten Materialpalette. Es besteht daher die dringende Notwendigkeit, die Materialien an diese verbreiteten Produktionsverfahren anzupassen, da lasergestützte Verfahren langfristig sowohl wegen ihres Durchsatzes als auch wegen ihrer Präzision wichtige Produktionsverfahren dominieren werden. Dies erfordert einen grundlegenden Forschungsansatz bereits am Beginn der Prozesskette, dem Material. Es besteht dringender Handlungsbedarf, die weltweite Spitzenposition Deutschlands in der Photonik und Materialwissenschaft zu verteidigen und weiter auszubauen. Ein koordiniertes, kohärentes, erstmals die Materialentwicklung und Photonikforschung vereinendes, bereits bei der Materialsynthese ansetzendes Forschungsprogramm soll zur Ausschöpfung dieses erheblichen Potenzials beitragen. Um eine Rückkopplung zwischen Prozessverhalten und Materialeigenschaft sicherzustellen, werden im Rahmen des Schwerpunktprogrammes 2122 seit 2018 Tandemprojekte mit mehr als 25 Arbeitsgruppen sowie internationalen Mercator Fellows aus den Bereichen „Materialien“ und „Laserprozess“ durch die DFG gefördert. Die wissenschaftlichen Fragestellungen sind materialübergreifend formuliert und auf das photonische Verfahren der pulverbasierten additiven Laserfertigung konzentriert. Eine solch große fächerübergreifende Studie ermöglichte zudem erstmals eine umfassende Interlabo-ratory Study einschließlich Forschungsdatenmanagement. Der Vortrag stellt den interdisziplinären Forschungsansatz sowie ausgewählte Ergebnisse des SPP 2122 vor und unterstreicht damit die Bedeutung einer systematischen Materialentwicklung für die Zukunft der additiven Fertigung.
12.00 h Werkstoff-Konzepte für den Uhren- und Schmuckbereich
Innovative Werkstoff-Konzepte sowie Verfahrenstechnologien sind im Uhren- und Schmuckbereich immer gefragt, insbesondere im Hinblick auf Designfreiheit, Ästhetik, Funktionalität aber auch Nachhaltigkeit. Pulvertechnologische Verfahren auf Basis von druck-unterstützten Sintertechnologien bzw. die additive Fertigung ermöglichen die Herstellung von speziellen Werkstoffkombinationen oder die Realisierung von komplexen Geometrien. Durch gezielte Auswahl der Rohstoffe sowie entsprechender Legierungsentwicklungen lassen sich mechanische Eigenschaften, Korrosionsverhalten und Farbgebung anpassen. Materialien wie Titan, Edelmetalle aber auch der Einsatz von Keramikpulver eröffnen dabei eine Reihe von Möglichkeiten. Die Kombination aus Funktion und Ästhetik macht pulverbasierte Technologien besonders attraktiv für hochwertige Anwendungen, speziell, wenn es auch um Multi-Material-Kombinationen geht.
12.30 h Flexible Werkstoffentwicklung für die additive Fertigung nach dem Pulverbaukastenprinzip
Das Laser-Pulverbettschmelzen (PBF-LB) ist eines der wichtigsten additiven Fertigungsverfahren und zeichnet sich durch eine sehr hohe Flexibilität in Bezug auf die geometrische Freiheit aus. Im Hinblick auf die zu verarbeitenden Werkstoffe ist diese Flexibilität bei PBF-LB jedoch noch nicht gegeben; im Allgemeinen steht nur eine begrenzte Auswahl an Standardlegierungen zur Verfügung. Pulver für Spezialanwendungen sind daher oft sehr teuer. Ein neuer Ansatz zur Erweiterung des Materialspektrums für die additive Fertigung ist das Prinzip des Pulverbaukastens. Dabei können verschiedene Standardpulver miteinander, mit elementaren Pulvern oder anderen Zusätzen wie Karbiden oder Nitriden gemischt werden, um neue Legierungskonzepte und Werkstoffe herzustellen. Die Legierungsbildung findet dann während des PBF-LB-Prozesses in-situ statt. In diesem Vortrag werden einige Beispiele dafür gezeigt, wie Pulvermischungen zur Anpassung und Entwicklung von Werkstoffen verwendet werden können. Darüber hinaus werden die Herausforderungen diskutiert, die bei der Arbeit mit Pulvermischungen im PBF-LB-Verfahren noch zu bewältigen sind.
13.00 h Kurzpräsentation einzelner Aussteller
13.15 h Mittagessen und Besichtigung der Ausstellung
14.30 h Kurzvorträge (5 ausgewählte Poster)
15.30 h Posterausstellung mit Diskussion (Foyer Stadthalle) sowie Besichtigung der Ausstellung und Kaffeepause
16.30 h Substitution von Seltenerdmagneten durch Hartferrite in der Sensorik
Bei Zukunftstechnologien sind magnetische Werkstoffe von strategischer Bedeutung. Ob Elektromobilität, Windkraft oder Medizintechnik, in vielen Bereichen werden Magnete mit hoher Energiedichte benötigt. Hier haben sich in den letzten Jahrzehnten Magnete auf der Basis von Seltenerdmetallen etabliert. Seit der ersten Krise 2011 und heute wieder aktuell ist die Abhängigkeit bei diesen Rohstoffen von China allgemein bewusst. Während starke Motoren oder Generatoren ohne Seltenerdmagnete nur als elektrisch erregte Maschinen mit Kompromissen an Leistungsdichte auskommen, ist eine Substitution durch alternative Werkstoffe im Bereich der Sensorik durch die Entwicklung komplexer Magnetisierstrukturen heute möglich. Der Vortrag zeigt beispielhaft Lösungen mit kunststoffgebundenen Hartferriten, die sich schon in der Technik etabliert haben und motiviert zu einem Umdenken in der magnetischen Positionssensorik.
17.00 h Kaltsintern von oxidkeramischen Werkstoffen
Das Kaltsintern ermöglicht die Herstellung von Keramiken und Verbundwerkstoffen bei niedrigen Temperaturen (<300 °C) durch den gemeinsamen Einsatz von hohem Druck und der Zugabe einer flüssigen oder adsorbierten Phase (im einfachsten Fall reines Wasser), die als Sinterhilfe dient. Der Effekt des Kaltsinterns wurde bereits für mehr als 50 anorganische Zusammensetzungen bei Temperaturen beobachtet, bei denen normalerweise keine Verdichtung möglich ist. Die erfolgreiche Prozessierung und Einstellung der Eigenschaften von Hochleistungskeramiken durch Kaltsintern erfordert ein grundlegendes Verständnis der zugrunde liegenden Mechanismen. Das Kaltsintern hat das Potenzial, die Herstellung neuer Werkstoffkombinationen zu ermöglichen, die mit anderen Verfahren aufgrund der Temperaturdegradation nicht gesintert werden können. In diesem Vortrag werden mehrere Beispiele für kaltgesinterte Werkstoffe mit ungewöhnlichen Eigenschaften vorgestellt.
17.30 h Ende des ersten Tages
19.30 h Mercure Hotel: Geselliger Abend (Einlass 19.00 Uhr, Anmeldung erforderlich, nur in Verbindung mit Teilnahme am Hagener Symposium)
Freitag, 28.11.2025
9.00 h Moderne Diamantkristalle für die Bearbeitung von Keramik- und PM-Materialien
Zur Bearbeitung von harten Werkstoffen werden synthetisch hergestellte Diamant- und CBN-Kristalle in Bindungssystemen (Schleif-werkzeugen) oder lose eingesetzt. Diese Kristalle (Superabrasives) werden in speziell entwickleten HPHT-Synthesen produziert. Mit der HPHT (High Pressure High Temperature)-Synthese werden fast alle Diamant- und CBN-Kristalle produziert. Ziel ist, einen superharten Kristall für den besten Bearbeitungsprozess harter Materialien wie Kermaik oder Hartmetallvarianten zu entwickeln. Hierbei sind Kristallwuchs, Kornform und Bruchverhalten wichtige Parameter. Für eine bessere Einbindung in verschiedene Bindungssysteme stehen Coatings zur Verfügung.
9.30 h Präzisionsschmieden: Potenziale und Herausforderungen beim endkonturnahen Schmieden
Das Gesenkschmieden ist ein etabliertes Produktionsverfahren zur Herstellung hochbeanspruchbarer Bauteile in mittleren bis hohen Stückzahlen. Aufgrund der extremen Prozessbedingungen sind meist nachgelagerte Prozessschritte zur Steigerung der Präzision sowie Aufmaße notwendig. Beim Präzisionsschmieden werden Funktionsflächen hingegen bereits in der Warmmassivumformung erzeugt. So werden Prozessketten verkürzt und Werkstoff und Energie eingespart. Im Rahmen des Vortrages werden die Grundlagen, der Stand der Technik sowie die Herausforderungen und Limitierungen des Präzisionsschmiedens vorgestellt. Zudem wird die Frage diskutiert, ob die Potentiale des Präzisionsschmiedens ausreichen, um eine Konkurrenz zur Pulvermetallurgie darzustellen und welche Synergien sich aus der Kombination dieser Technologien ergeben können.
10.00 h SMART - „Intelligente“ Wolframlegierungen für Fusions- und Solarkraftwerke
Dr. Fritsch Sondermaschinen GmbH, Fellbach
Neue Energiequellen, wie Magnetfusion, erfordern den Einsatz von Materialien, die Temperaturen von über 800 °C standhalten können. In zukünftigen Fusionskraftwerken gilt Wolfram als bevorzugtes Material für die Plasmawand. Ein Nachteil von reinem Wolfram ist die starke Oxidation im Störfall (Lufteinbruch in die Reaktorkammer), die ein erhebliches Sicherheitsrisiko darstellt. Eine Lösung bieten SMART-Legierungen (Self-passivating Metal Alloy with Reduced Thermo-oxidation). Besonders hervorzuheben ist Oxidationsbeständigkeit von SMART: Im Vergleich zu reinem Wolfram weisen SMART eine um 10⁴-fach geringere Oxidationsrate bei
1000 oC auf. Die Herstellung vom SMART erfolgt durch mechanisches Legieren in Kombination mit feldunterstützter Sintertechnologie (FAST) und eröffnet neue Möglichkeiten der Additiven Fertigung. Derzeit läuft die Industrialisierung der SMART-Technologie. Der Vortrag gibt einen Überblick über die SMART-Technologie und ihre Anwendungen in der Fusion sowie in der Solarthermie.
10.30 h Besichtigung der Ausstellung und Kaffeepause
11.00 h Hartmetalle - Das Zusammenspiel von Leistung und Nachhaltigkeit
Prof. Dr. Ralph Useldinger*, Université du Luxembourg, Dr. Uwe Schleinkofer, Dr. Christoph Czettl, CERATIZIT Austria GmbH, Reutte/Österreich, Laurent Federspiel, Tobias Schöttl, Dr. Fadik Aslan, CERATIZIT Luxembourg S.à r.l., Mamer/Luxemburg, Teemu Karhumaa, GTP, Jyväskylä/Finnland
Hartmetalle werden in Anwendungen, wie Zerspanwerkzeugen und Verschleißschutzlösungen, höchsten Anforderungen ausgesetzt. Dabei müssen vielfältige Materialeigenschaften berücksichtigt werden, um den unterschiedlichen Einsatzgebieten gerecht zu werden. Traditionell wurden empirische Methoden zur Optimierung der Werkstoffeigenschaften verwendet. Heutzutage kommen zunehmend maschinelles Lernen und Simulationstechniken wie FEM (Finite-Elemente-Methode), DEM (Diskrete-Elemente-Methode), CFD (Computational Fluid Dynamics) und CalPhaD (Calculated Phase
Diagrams) zum Einsatz. Zusätzlich müssen wirtschaftliche und umwelttechnische Anforderungen in Einklang gebracht werden. In diesem Vortrag werden diese komplexen Einflussfaktoren beleuchtet.
11.30 h Moderne Technologien und Werkstoffe für Hartmetallschichten
Hartmetalle und weitere Hartstoff-Binder-Verbundwerkstoffe haben eine herausragende Bedeutung in der Oberflächentechnik. In zahlreichen Anwendungen erlauben durch Thermisches Spritzen oder Auftragschweißen aufgebrachte Beschichtungen eine Vervielfachung der Lebensdauer tribologisch belasteter großer Bauteile und somit Produktivitätssteigerungen. Im Bereich des Thermischen Spritzens ermöglicht das Hochgeschwindigkeitsflammspritzen das Herstellen besonders dichter, harter, zäher und gut haftender Schichten, die infolge von Druckeigenspannungen insbesondere für dynamisch belastete Bauteile vorteilhaft sind. Unter den Auftragschweißverfahren zeichnet sich das Laser Cladding durch eine unübertroffene Prozessstabilität und Präzision aus. Neben den traditionellen Hartstoffen WC, W2C/WC (Wolframschmelzcarbid) und – im Gegensatz zum Sinterhartmetall – Cr3C2, die zumeist mit Matrices auf Cobalt- oder Nickelbasis kombiniert werden, finden vermehrt auch TiC(N) und NbC, vielfach in Kombination mit Matrices auf Eisenbasis, Einsatz.
12.00 h Herstellung und Schichteigenschaften neu-artiger Metalldiborid-CVD-Hartstoffschichten
Die Synthese von dünnen Metalldiborid-Schichten hat in den letzten Jahren großes Interesse geweckt, was vor allem an ihren außergewöhnlichen Eigenschaften liegt. Bor bildet mit den meisten Metallen binäre Verbindungen, die sich durch hohe Schmelztemperaturen, Härte und thermische Stabilität sowie chemische Inertheit auszeichnen. Neuartige Metalldiborid-Schichten der Metalle Zr und Hf sowie binäre und ternäre Mischborid-Schichten im System Zr-Hf-Ti-B werden in einem Niederdruck-CVD-Prozess im Temperaturbereich von 800 bis 1000 °C unter Nutzung der Metalltetrachlorid-Precursoren MeCl4 (Me = Zr, Hf oder/und Ti) sowie BCl3, H2 und Ar erzeugt. Die Schichten weisen hohe Härten von bis zu 38 GPa auf und erreichen deutlich höhere Standzeiten als aktuelle CVD-TiB2-Schichten.
12.30 h Schlusswort
Dr.-Ing. Johannes Pötschke, Fraunhofer IKTS Dresden
12.45 h Mittagessen
13.30 h Ende der Veranstaltung
Mitglieder des Programmausschusses 2025
TU Dortmund – ISF
Prof. Dr. Martin Bram
Forschungszentrum Jülich GmbH – IMD-2
Prof. Dr.-Ing. Christoph Broeckmann
RWTH Aachen – IWM
Univ.-Prof. i. R. Herbert Danninger
TU Wien, Institut für Chemische Technologien und Analytik
Dr.-Ing. Tim Gestrich
Fraunhofer IKTS Dresden
Univ. Prof. Dr. Christian Gierl-Mayer
TU Wien, Institut für Chemische Technologien und Analytik
Dr. rer. nat. Sebastian Boris Hein
Fraunhofer IFAM Bremen
Dipl.-Oec. Dirk Hölscheid
Fachverband Pulvermetallurgie e.V.
Dr.-Ing. Anke Kaletsch
RWTH Aachen – IWM
Dr.-Ing. Johannes Pötschke (Vorsitz)
Fraunhofer IKTS Dresden
Dr. Jürgen Schmidt
Boehlerit GmbH & Co. KG
Dr.-Ing. Markus Schneider
GKN Powder Metallurgy GmbH
Prof. Dr.-Ing. Thomas Weißgärber
Fraunhofer IFAM Dresden
Begleitende Fachausstellung
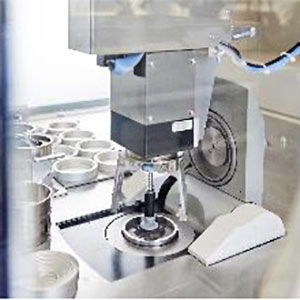
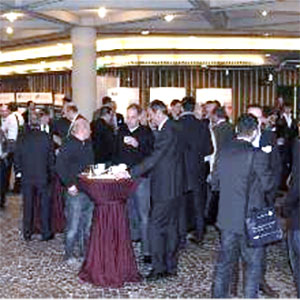
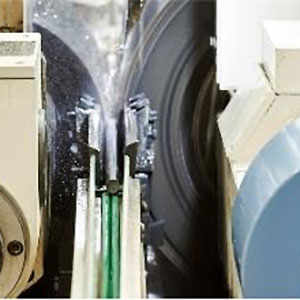
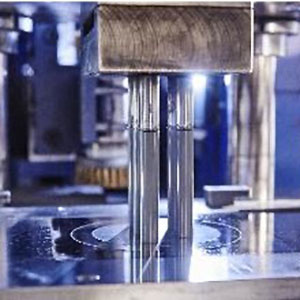
Anmeldung
„PULVER | METALLURGIE | ZUKUNFT“
27. bis 28. November 2025
Tagungsort und Tagungsbüro
Stadthalle Hagen
Wasserloses Tal 2, 58093 Hagen
* Pflichtfelder
Anmeldeformular
Beachten Sie folgende Informationen
² einschl. 2 Mittagessen, Pausengetränke, Tagungsband (nur PDF-Version), ohne „Geselliger Abend“ (bitte senden Sie Ihren Studentenausweis an info@pulvermetallurgie.com)
³ Teilnahme begrenzt (nur in Verbindung mit Teilnahme am 43. Hagener Symposium)
Durch diese Anmeldung erklären Sie sich mit der Speicherung Ihrer personenbezogenen Daten zum Zwecke der Veranstaltungsabwicklung und zur Veröffentlichung im Teilnehmerverzeichnis einverstanden. Es gelten die Datenschutzbedingungen sowie folgende Teilnahmebedingungen:
Eine Rechnung erhalten Sie nach Eingang Ihrer Anmeldung. Diese gilt gleichzeitig als Anmeldebestätigung. Durch diese Anmeldung erklären Sie sich mit der Speicherung Ihrer personenbezogenen Daten zum Zwecke der Veranstaltungsabwicklung und zur Veröffentlichung im Teilnehmerverzeichnis einverstanden. Im Rahmen der Veranstaltung sind die dann geltenden Hygienevorschriften/Hausordnungen des Veranstalters, der Stadthalle und des MERCURE Hotels Hagen zu beachten. Die Tagungsunterlagen mit Tagungsband (PDF bzw. Print on Demand) werden Ihnen zu Beginn der Veranstaltung ausgehändigt. Bei Ihrer Stornierung bis zum 30.10.2025 (Datum des Poststempels) wird Ihnen die Teilnahmegebühr abzgl. € 25,– für Bearbeitungskosten erstattet. Bei Ihrer Stornierung nach dem 30.10.2025 (auch aus Krankheitsgründen) kann leider keine Erstattung mehr erfolgen. Sie haben jedoch die Möglichkeit, einen Ersatzteilnehmer zu benennen. Die Tagungsunterlagen werden Ihnen andernfalls nach Beendigung der Veranstaltung in elektronischer Form zum Download bereitgestellt oder zugesandt (bei Print on Demand-Tagungsband). Der Veranstalter behält sich das Recht vor, die Veranstaltung mit einer Frist von 14 Tagen abzusagen. Bis dahin gezahlte Gebühren werden in diesem Falle zurückerstattet. Weitergehende Entschädigungsleistungen werden in diesem Falle nicht gewährt.
Hagener Symposium
Tagungsort und Tagungsbüro
Stadthalle Hagen, Wasserloses Tal 2, 58093 Hagen
Kontakt
Goldene Pforte 1 ● 58093 Hagen (Emst)
Telefax: +49 (0) 2331 958717